
fabric formwork. cloud 9 projects. Concrete design, architecture, Concrete formwork
ABSTRACT. Since its invention by the Romans, concrete has been cast into all manner of formworks whether temporary or permanent. Concrete members have traditionally been cast using a rigid formwork and engineering analysis has been on prismatic members. All rigid formworks including rubble, brick, and wood have become the containment form of.

Stretch Concrete Sink, Fabric formed Concrete Sink Molds, Concrete Tools, Concrete Bathroom
Editor's Note: With this Guide to Fabric-Formed Concrete it is hoped that existing and new techniques that may come along can be documented here for the benefit of others who wish to use this truly unique method of forming concrete for their projects.The Table of Contents shown below contain topics similar to ACI's SP-4 Formwork for Concrete as it is assumed there will be many similar.

Fabric Formed Concrete
Fabric formed concrete is the result of pumping a highly fluid concrete mix into specially woven fabric "forms." This method of erosion control allows for fast, economical construction of countless applications. At US FUSION, we offer exceptional installation of fabric formed concrete, with the highest attention to quality and detail..
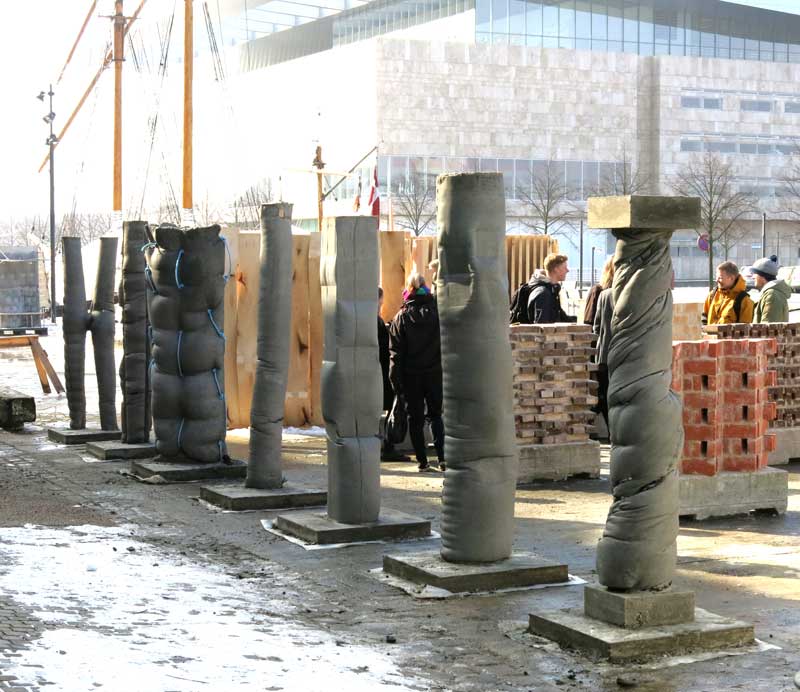
CONCRETELY FabricFormed Concrete Columns
ARMORFORM® Fabric-Formed Concrete Revetment Systems. The ARMORFORM® erosion control system utilizes double-layer woven geotextiles engineered exclusively to serve as forms for casting concrete erosion control revetments and linings. The forms are woven from nylon and/or polyester yarns and are designed with the required mechanical and.

GFRC & FabricFormed Concrete — Concrete Design School
What is Fabric Formed Concrete? Hard Armor is a term used to describe permanent stabilization solutions, which exist in many forms, both vegetated and non-vegetated. Such solutions are indicated when water velocities in channels or ditches require very robust reinforcement to prevent erosion problems.
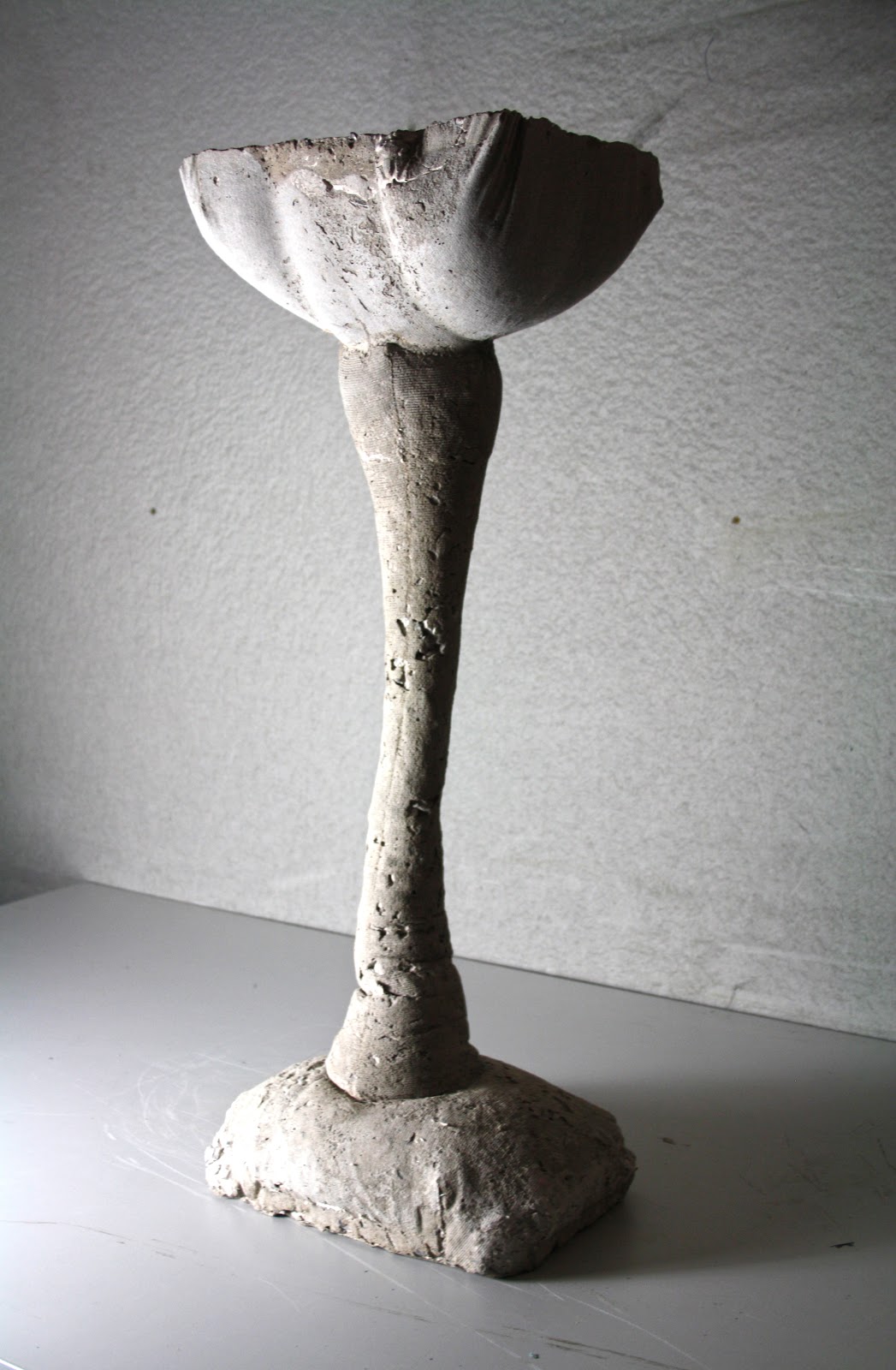
Fabric Formed Concrete Column Mark T Clarkson Architectural Masters Thesis Blog
Fabric formed concrete liners are highly engineered textiles fabricated into custom panel sections and patterns consisting of durable concrete grout. These liners improve performance across various applications, including erosion control and scour protection, as well as environmental, foundation, and marine construction..

MArch 200809 Fabric Formed Concrete Concrete, Concrete design, Design
Architects and designers in Japan, Korea, Canada and the United States have begun to use flexible fabric formworks made from geotextile fabric to form concrete members for their projects, Schmitz.

Material Reduction Efficient FabricFormed Concrete, Winnipeg
Fabric formed concrete allows us to create shapes that would otherwise be impossible, too time intensive or cost prohibitive to construct any other way. Fabric forming inherently creates natural shapes - relatable shapes. They are human in nature so we see ourselves in them. Fabric-forming, when done with finesse and restraint, yields a.

Fabric Formed Concrete
Significant among the early innovators were James H. de W. Waller (1884-1968) who in 1934 patented a fabric-formed system using hessian (burlap) fabric for numerous building components and in 1948.
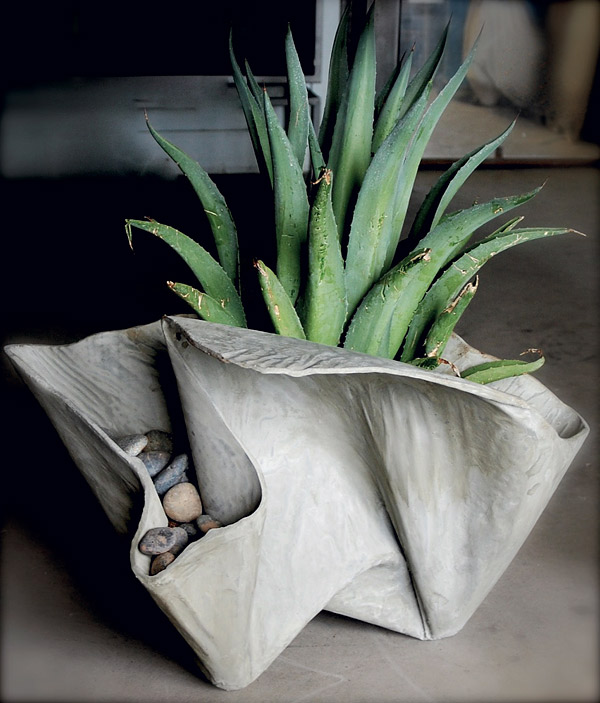
10 Unusual Concrete Creations Concrete Decor
We will take a look at those engineers, architects, designers and researchers who have made use of this unique way of forming concrete. Developed and patented by Construction Techiques, Inc. in the mid-1960's Fabriform® is the original fabric-formed concrete system. Their products include Articulated Block, Filterpoint, Unimat, Concrete Bags.

Fabric formed concrete retaining wall Concrete architecture, Concrete texture, Concrete design
Fabriform® is a simple and cost-effective method of erosion control. This system has allowed for fast and economical construction of erosion protection for over 50 years. Fabriform® was developed and patented by Construction Techniques, Inc in the mid-1960s and is still the leading manufacturer of high-quality, fabric-formed concrete revetments.
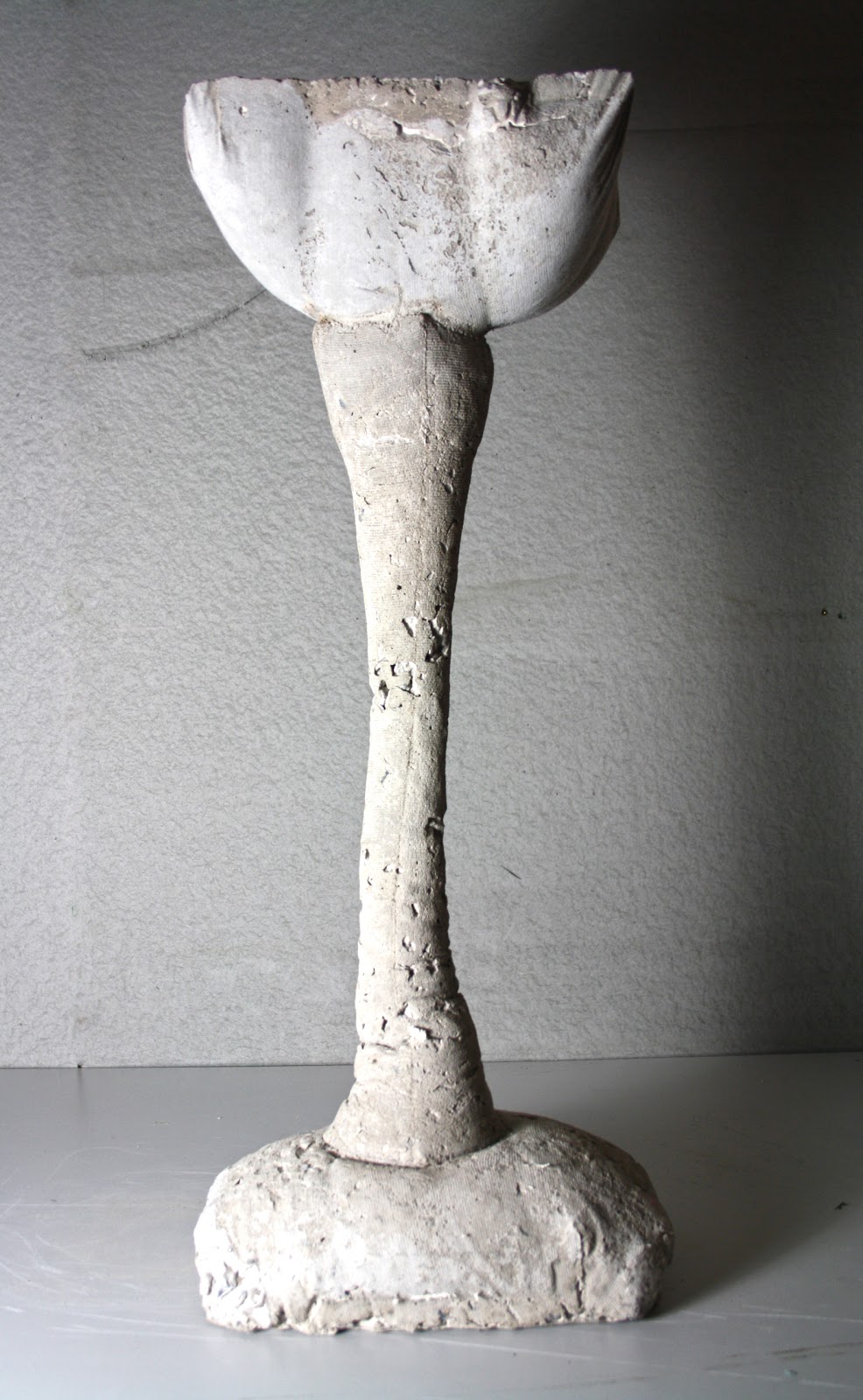
Fabric Formed Concrete Column Mark T Clarkson Architectural Masters Thesis Blog
Kenzo Unno. Another architect whose work has softened up concrete is Japanese architect Kenzo Unno. Working independently of Fisac he has developed several cast-in-place (CIP) fabric-formed wall systems since the mid 1990's. The Kobe earthquake on January 17, 1995 provided the motivation for Unno to create residential designs that are.
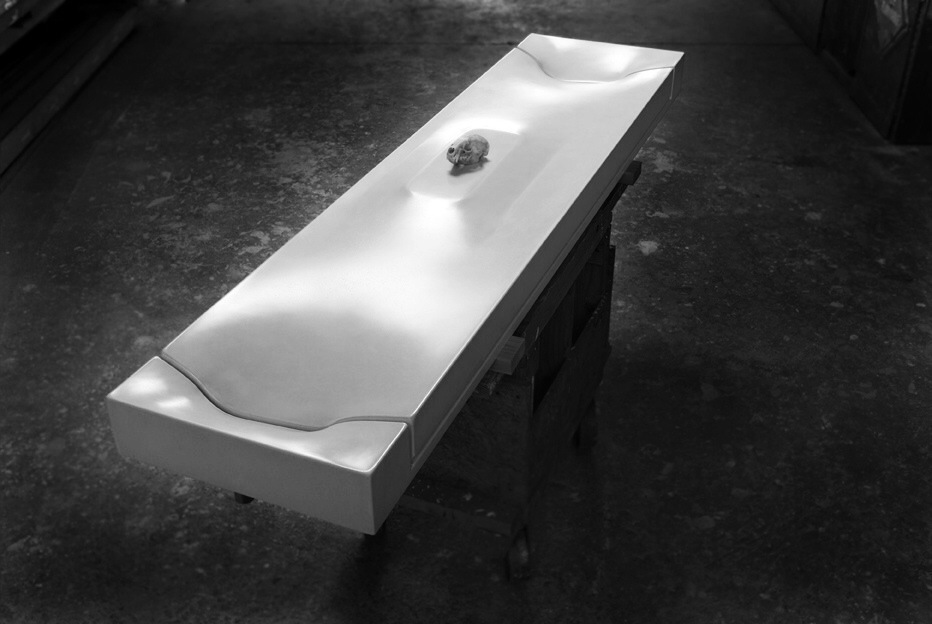
GFRC & FabricFormed Concrete — Concrete Design School
Fabric formwork is a building technology that employs geotextile fabrics as the formwork material for concrete construction. Its first application can be attributed to Gustav Lilienthal, a builder, and inventor, who combined his knowledge in textiles with construction to invent a fabric-formed suspended floor.
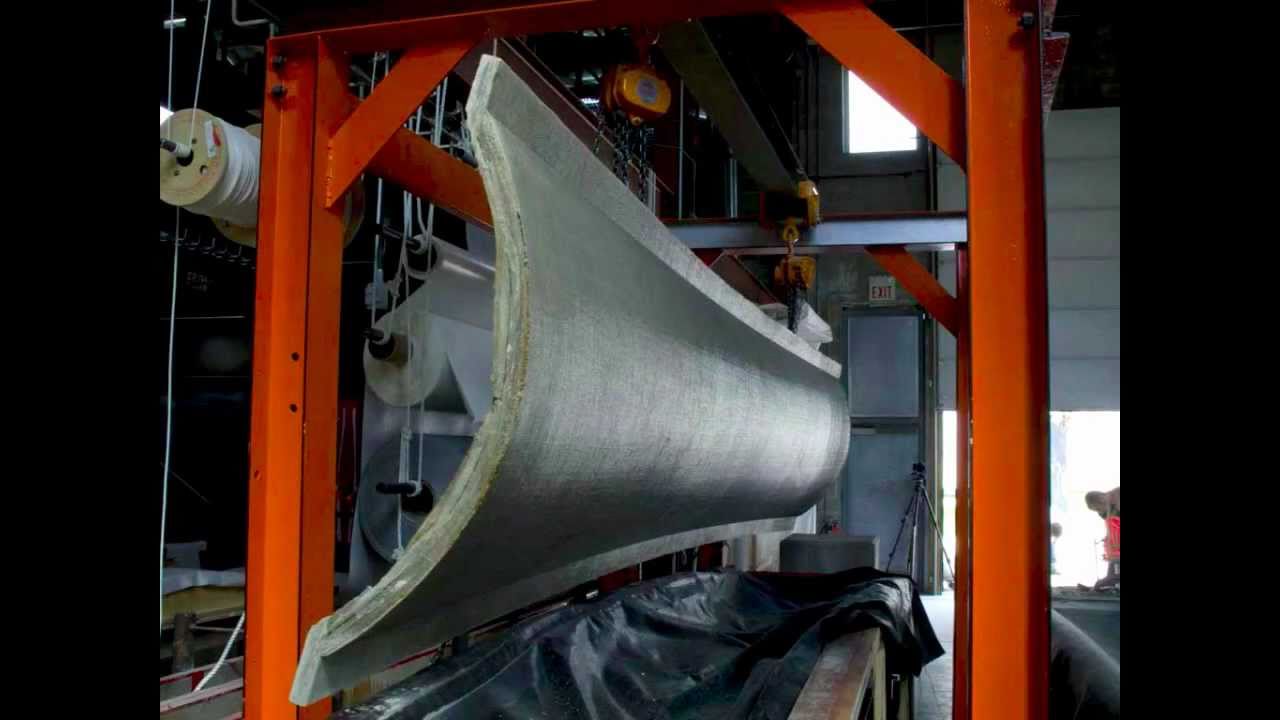
Heavy Light FabricFormed Concrete Structures YouTube
The Manufacturer of HYDROTEX® Fabric Formed Concrete Erosion Control Systems. Synthetex is the manufacturer of HYDROTEX® fabric-formed concrete mattresses, the top permanent erosion control solution for bridges, rivers, canals, and more. A leader in the use in a diverse range of markets and environments, HYDROTEX® fabric-formed concrete is.

Material Reduction Efficient FabricFormed Concrete, Winnipeg Concrete design, Concrete
HYDROTEX fabric-formed concrete is the better alternative to concrete slope paving, saving your company precious resources and time. Get a project estimate today: Submit a quick form. Call us now. HYDROTEX fabric-formed concrete is the top solution for lining trapezoidal channels in any facility or industry.

CONCRETELY FabricFormed Concrete Columns Formas Project Concrete Formwork Pinterest
Fabric-formed concrete members are easy to form, immaculate in finish (Figure 1), organic in form, and inexpensive to produce. The surface finish of concrete formed in wood, steel or plastic molds generally has imperfections, often requiring further touch ups and costly treatments (Figure 2). Lumber and plywood used for conventional concrete.